Техническая диагностика оборудования
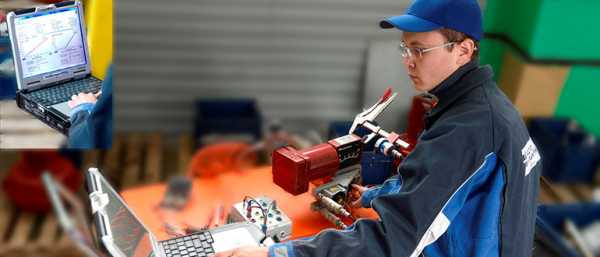
Диагностика оборудования – это осмотр техустройства на предмет выявления в нем определенных неполадок. В ходе диагностики могут быть обнаружены и устранены такие явления, как повреждения оболочек, сильный износ, неверное функционирование и наличие дефектов.
Техническая диагностика
Любое производство использует аппаратуру различной степени сложности. Для бесперебойного цикла работы и гарантии безопасности людей нужно проводить регулярную техническую диагностику. Данная процедура является первой в цепочке проведения экспертизы для оценки безопасности технологических устройств производства. Во время диагностики станет ясно, отвечает или не отвечает проверяемый объект нормативам и требованиям охраны труда. Кроме этого, своевременное тестирование оборудования позволит избежать приобретения некачественного или устарелого оборудования. Часто под видом новых машин пытаются продать контрафактные объекты. Их также поможет выявить техническая диагностика.
Наука и техника развиваются невероятными темпами, потому уже сейчас существуют усовершенствованные методы для диагностики рабочих систем. Теперь за короткий срок можно получить полную картину о состоянии определенной машины и избежать ее дальнейшего простоя. Иногда простой на предприятии может сильно снизить показатели всего производства. Поэтому диагностика должна проводиться быстро и результат озвучиваться сразу же.
Преимущества диагностики
Техническое диагностирование промышленных машин имеет ряд преимуществ, и должно проводиться в таких целях:
- определение срока их службы;
- установление ресурса для безопасной работы;
- устранение мелких неполадок;
- профилактика изнашивания деталей;
- определение уровня износа отдельных элементов.
Любое техническое оборудование, установленное на производстве, имеет свой паспорт безопасности, который должен соответствовать реальному положению вещей. Профилактический осмотр рабочих элементов предупреждает возникновение серьезных аварий. Проверка оборудования проводится с помощью установленных методов, а именно: измерительного и визуального контроля.
yugpm.com
7. Диагностика технического состояния оборудования
7.1. Основные принципы технического диагностирования
Диагностика — отрасль науки, изучающая и устанавливающая признаки состояния системы, а также методы, принципы и средства, при помощи которых дается заключение о характере и существе дефектов системы без ее разборки и производится прогнозирование ресурса системы.
Техническая диагностика машин представляет систему методов и средств, применяемых при определении технического состояния машины без ее разборки. При помощи технической диагностики можно определять состояния отдельных деталей и сборочных единиц машин, производить поиск дефектов, вызвавших остановку или ненормальную работу машины.
На основе полученных при диагностике данных о характере разрушения деталей и сборочных единиц машины в зависимости от времени ее работы техническая диагностика позволяет прогнозировать техническое состояние машины на последующий срок работы после диагностирования.
Совокупность средств диагностирования, объекта и исполнителей, действующих по установленным алгоритмам, называется системой диагностирования.
Алгоритм — это совокупность предписаний, определяющих последовательность действий при диагностировании, т.е. алгоритм устанавливает порядок проведения проверок состояния элементов объекта и правила анализа их результатов. Причем безусловный алгоритм диагностирования устанавливает заранее определенную последовательность проверок, а условный — в зависимости от результатов предыдущих проверок.
Техническое диагностирование — это процесс определения технического состояния объекта с определенной точностью. Результатом диагностирования служит заключение о техническом состоянии объекта с указанием при необходимости места, вида и причины дефекта.
Диагностирование — один из элементов системы ТО. Основная его цель — достижение максимальной эффективности эксплуатации машин и, в частности, сведение до минимума затрат на их ТО. Для этого дают своевременную и квалифицированную оценку технического состояния машины и разрабатывают рациональные рекомендации по дальнейшему использованию и ремонту сборочных .единиц (обслуживанию, ремонту, дальнейшей эксплуатации без обслуживания, замене сборочных единиц, материалов и т.п.).
Диагностирование проводят как при ТО, так и при ремонте.
При ТО задачи диагностирования заключаются в том, чтобы установить потребность в проведении капитального или текущего ремонта машины или ее сборочных единиц; качество функционирования механизмов и систем машин; перечень работ, которые необходимо выполнить при очередном техническом обслуживании.
При ремонте машин задачи диагностирования сводятся к выявлению сборочных единиц, подлежащих восстановлению, а также оценке качества ремонтных работ. Виды технического диагностирования классифицируют по назначению, периодичности, месту проведения, уровню специализации (табл. 7.1). В зависимости от парка машин диагностирование проводят силами Эксплуатационного предприятия или на специализированных предприятиях технического сервиса.
Диагностирование, как правило, совмещают с проведением работ по ТО. Кроме того, при возникновении отказов машины проводят углубленное диагностирование по заявке оператора.
В последнее время появилась сеть малых предприятий по оказанию услуг технического сервиса машин, в том числе и диагностирования, т.е. диагностирование в этом случае выводится из состава работ по ТО и становится самостоятельной услугой (товаром), которая оказывается по заявке клиента как в период эксплуатации, так и при оценке качества ремонта, остаточной стоимости работ по восстановлению работоспособности и исправности машин, а также при купле и продаже машин, бывших в употреблении.
Работы по диагностированию на эксплуатационном предприятии проводятся в зависимости от размера и состава парка машин на специализированном участке (посту) диагностирования или на участке (посту) ТО. Объектом технической диагностики может быть техническое устройство или его элемент. Простейшим объектом технической диагностики будет кинематическая пара или сопряжение. Однако в класс рассматриваемых объектов может быть включен агрегат любой сложности. Диагностируемый объект можно рассматривать в двух аспектах: с точки зрения структуры и способа функционирования. Каждый из аспектов имеет особенности, описываемые своей системой понятий.
Под структурой системы понимается определенная взаимосвязь, взаиморасположение составных частей (элементов), характеризующих устройство и конструкцию системы.
Параметр — качественная мера, характеризующая свойство системы, элемента или явления, в частности процесса.
Объективные методы диагностирования дают точную количественную оценку сборочной единицы, машины. Они основаны на использовании как специальных контрольно-диагностических средств (оборудования, приборов, инструмента, приспособлений), так и устанавливаемых непосредственно на машинах или входящих в комплект инструмента машиниста.
Таблица 7.1
Виды диагностирования и области их применения
Квалифицирующий признак | Вид диагностирования | Область применения | Основные задачи |
По месту диагностирования По объемуПо периодичности По уровню специализации | Эксплуатационное Производственное Полное Частичное Плановое (регламентированное) Внеплановое (причинное) Специализированное Совмещенное | При техническом обслуживании, осмотрах, возникновении отказов и неисправностей При ремонте машин на ремонтных предприятиях При входном и выходном контроле машин в ремонтном производстве При технических осмотрах При периодическом ТО и осмотрах При возникновении отказов и неисправностей При обслуживании машин на сервисных предприятиях и силами ЦБПО При ремонте машин При обслуживании машин эксплуатационным предприятием и силами ЦБПО | Определение остаточного ресурса сборочных единиц и потребности в регулировочных работах. Установление объема и качества ремонтных работ, обнаружение неисправностей, оценка готовности машин к работам Определение остаточного ресурса сборочных единиц. Контроль качества ремонтных работ Определение остаточного ресурса сборочных единиц, проверка качества их функционирования, выявление перечня регулировочных работ, предотвращение отказов Определение перечня необходимых регулировочных работ, проверка готовности машин к работе или качества их хранения, выявление неисправностей с последующим их устранением Предотвращение отказов, определение остаточного ресурса, установление перечня регулировочных работ, проверка качества обслуживания и ремонта машин Выявление отказов и неисправностей с последующим их устранением Проведение диагностирования, предусмотренного ТО-3 и после межремонтной наработки Определение остаточного ресурса сборочных единиц, проверка качества ремонта Диагностирование с последующим обслуживанием машины, проверка потребности машин в ремонте с устранением дефектов. Выявление и устранение дефектов при возникновении отказов |
Объективное диагностирование разделяют на прямое и косвенное
Прямое диагностирование — это процесс определения технического состояния объекта по его структурным параметрам (зазорам в подшипниковых узлах, в клапанном механизме, в верхних и нижних головках шатунов кривошипно-шатунного механизма, биению валов, размерам деталей, доступных для непосредственного измерения, и др.).
Сборочные единицы и машину в целом диагностируют по структурным параметрам с помощью универсальных измерительных приборов: калибров, щупов, масштабной линейки, штангенциркулей, микрометров, зубометров, нормалемеров и др. Это позволяет получать точные результаты. Недостаток такого метода заключается в том, что он во многих случаях требует разборки объекта диагностирования. Последнее значительно увеличивает трудоемкость работ и нарушает приработку сопряженных поверхностей. Поэтому в практике прямое диагностирование, как правило, проводят в тех случаях, когда структурные параметры объекта диагностирования можно замерить без разборки сопряженных поверхностей.
Косвенное диагностирование — это процесс определения фактического состояния объекта диагностирования по косвенным, или, как их называют, диагностическим параметрам.
В качестве косвенных показателей используют изменение параметров рабочих процессов, структурных шумов, содержания продуктов износа в масле, мощности, расхода топлива и др.
Сам процесс диагностирования проводят с помощью манометров, вакуумметров, пьезометров, расходомеров, пневматических калибраторов, дымомеров и различных специальных приборов.
studfiles.net
3.3. Техническая диагностика оборудования. Система технического обслуживания и ремонта общепромышленного оборудования : Справочник
3.3. Техническая диагностика оборудования
3.3.1. Техническое диагностирование (ТД) – элемент Системы ППР, позволяющий изучать и устанавливать признаки неисправности (работоспособности) оборудования, устанавливать методы и средства, при помощи которых дается заключение (ставится диагноз) о наличии (отсутствии) неисправностей (дефектов). Действуя на основе изучения динамики изменения показателей технического состояния оборудования, ТД решает вопросы прогнозирования (предвидения) остаточного ресурса и безотказной работы оборудования в течение определенного промежутка времени.
3.3.2. Техническая диагностика исходит из положения, что любое оборудование или его составная часть может быть в двух состояниях – исправном и неисправном. Исправное оборудование всегда работоспособно, оно отвечает всем требованиям ТУ, установленных заводом-изготовителем. Неисправное (дефектное) оборудование может быть как работоспособно, так и неработоспособно, т. е. в состоянии отказа.
3.3.3. Оборудование может отказать в связи с изменением внешней среды и по причине физического износа деталей, находящихся как снаружи, так и внутри оборудования. Отказы являются следствием износа или разрегулировки узлов.
3.3.4. Техническая диагностика направлена в основном на поиск и анализ внутренних причин отказа. Наружные причины определяются визуально, при помощи измерительного инструмента, несложных приспособлений.
Методы, средства и рациональная последовательность поиска внутренних причин отказа зависят от сложности конструкции оборудования, от технических показателей, определяющих его состояние. Особенность ТД состоит в том, что она измеряет и определяет техническое состояние оборудования и его составных частей в процессе эксплуатации, направляет свои усилия на поиск дефектов.
3.3.5. По величине дефектов составных частей (агрегатов, узлов и деталей) можно определить работоспособность оборудования. Зная техническое состояние отдельных частей оборудования на момент диагностирования и величину дефекта, при котором нарушается его работоспособность, можно предсказать срок безотказной работы оборудования до очередного планового ремонта, предусмотренного нормативами периодичности Системы ППР, а также необходимость их корректировки.
3.3.6. Заложенные в основу ППР нормативы периодичности являются опытно усредненными величинами, установленными так, чтобы ремонтные периоды были кратными и привязанными к календарному планированию основного производства (год, квартал, месяц).
3.3.7. Любые усредненные величины имеют свой существенный недостаток: даже при наличии ряда уточняющих коэффициентов они не дают полной объективной оценки технического состояния оборудования и необходимости вывода в плановый ремонт. Почти всегда присутствуют два лишних варианта: остаточный ресурс оборудования далеко не исчерпан, остаточный ресурс не обеспечивает безаварийную работу до очередного планового ремонта. Оба варианта не обеспечивают требование Федерального закона № 57-ФЗ об установлении сроков полезного использования основных фондов путем объективной оценки потребности его постановки в ремонт или вывода из дальнейшей эксплуатации.
3.3.8. Объективным методом оценки потребности оборудования в ремонте является постоянный или периодический контроль технического состояния объекта с проведением ремонтов лишь в случае, когда износ деталей и узлов достиг предельной величины, не гарантирующей безопасной, безотказной и экономичной эксплуатации оборудования. Такой контроль может быть достигнут средствами ТД, а сам метод становится составной частью Системы ППР (контроля).
3.3.9. Другой задачей ТД является прогнозирование остаточного ресурса оборудования и установления срока его безотказной работы без ремонта (особенно капитального), т. е. корректировка структуры ремонтного цикла.
3.3.10. Техническое диагностирование успешно решает эти задачи при любой стратегии ремонта, особенно стратегии по техническому состоянию оборудования. В соответствии с этой стратегией работы по поддержанию и восстановлению работоспособности оборудования и его составных частей должны осуществляться на основе ТД оборудования.
3.3.11. Техническое диагностирование является объективным методом оценки технического состояния оборудования с целью определения наличия или отсутствия дефектов и сроков проведения ремонта, в том числе прогнозирования технического состояния оборудования и корректировки нормативов периодичности ремонта (особенно капитального).
3.3.12. Основным принципом диагностирования является сравнение регламентированного значения параметра функционирования или параметра технического состояния оборудования с фактическим при помощи средств диагностики. Под параметром здесь и далее согласно ГОСТ 19919—74 понимается характеристика оборудования, отображающая физическую величину его функционирования или технического состояния.
3.3.13. Целями ТД являются:
контроль параметров функционирования, т. е. хода технологического процесса, с целью его оптимизации;
контроль изменяющихся в процессе эксплуатации параметров технического состояния оборудования, сравнение их фактических значений с предельными значениями и определение необходимости проведения ТО и ремонта;
прогнозирование ресурса (срока службы) оборудования, агрегатов и узлов с целью их замены или вывода в ремонт.
3.3.14. Прогнозирование периодичности текущего и, особенно, капитального ремонта оборудования возможно лишь при одновременном ТД всех или большинства его составных частей.
3.3.15. Как показывает опыт, наиболее эффективное использование преимуществ ТД достигается тогда, когда на предприятии функционирует специальная задача «Диагностика оборудования», обеспеченная компьютерной техникой.
Несмотря на большое разнообразие применяемых для диагностирования оборудования приборов, монтажных схем датчиков, их конструкторского исполнения и т. д., как показывает отечественный и мировой опыт, подходы к внедрению ТД в практику остаются общими. В Приложении 8 кратко рассмотрена методика и приведен один из общих способов организации ТД на предприятии, а в табл. 3.1 указан перечень диагностических устройств, имеющихся в специальных передвижных ремонтных мастерских.
Таблица 3.1
Перечень диагностических устройств, находящихся в передвижных ремонтных мастерских
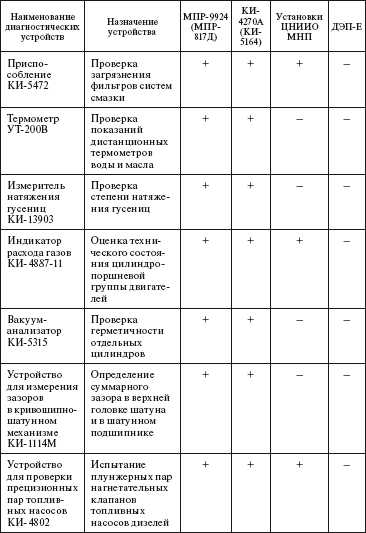
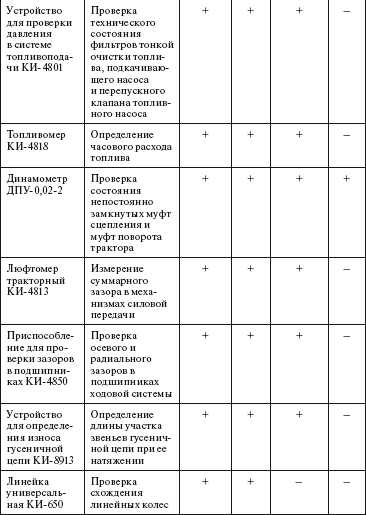
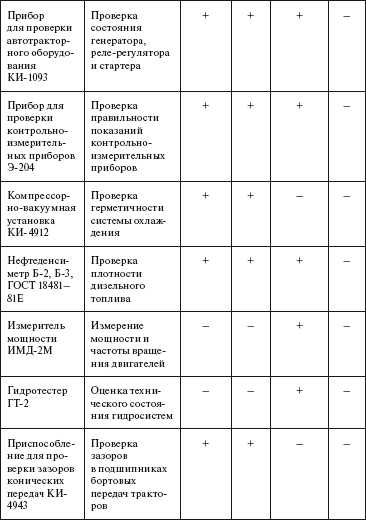
Следующая глава >
tech.wikireading.ru
техническая диагностика — это… Что такое техническая диагностика?
- техническая диагностика
- техни́ческая диагно́стика
-
один из способов проверки состояния и работоспособности технического изделия с целью выявления в нём скрытых и явных дефектов, неисправных узлов и элементов, отклонений от заданных условий и режима работы. Является одним из действенных средств обеспечения надёжности. Методы и приёмы технической диагностики подобны методам медицинской диагностики. Осуществляется вначале внешним осмотром изделия для выявления механических повреждений (царапин, вмятин, сколов, отверстий), нарушений тепло – и электроизоляции и антикоррозионного покрытия под воздействием света, влаги, тепла. Затем работоспособность изделия проверяют при помощи специальных датчиков и измерительных приборов, позволяющих установить соответствие или расхождение значений параметров действующего объекта с теми, что заданы в технических условиях. Проверка осуществляется как в обычных, так и в специально создаваемых условиях, близких к экстремальным для данных изделий.
По результатам диагностических исследований определяют надёжность данного изделия, его работоспособность и вероятность безотказной работы в течение определённого промежутка времени. В случае неисправности изделие ремонтируют (или заменяют отдельные узлы на новые) и настраивают на нужный режим работы. Диагностика сложных машин и устройств (напр., авиационных двигателей, автомобилей, прецизионных станков) осуществляется на диагностических стендах, специально оборудованных для комплексной всесторонней проверки исследуемого объекта. Компьютеризованное диагностическое оборудование позволяет за считанные минуты получить полную информацию не только о состоянии и работоспособности объекта, но также о всех дефектах (явных и скрытых) и способах их устранения. Техническая диагностика не только выявляет имеющиеся у объекта неисправности, но и прогнозирует появление отказов в будущем. Это особенно важно для объектов, от исправности которых зависят здоровье и жизнь многих людей.
Энциклопедия «Техника». — М.: Росмэн. 2006.
- Техническая диагностика
-
состояния ЛА — установление и изучение признаков, характеризующих наличие дефектов в ЛА (его системах, силовых установках, бортовом оборудовании), для определения его технического состояния, характера и причин нарушения нормального функционирования, выявления мест возникновения и закономерностей развития повреждений и отказов ЛА. Т. д. как раздел авиационной науки разрабатывает принципы и методы исследований и прогнозирования технического состояния ЛА, применения системы сбора полётной информации, бортовых и наземных средств контроля, а также диагностические алгоритмы (проверки и поиска). При диагностировании технического состояния ЛА используются оперативная и накапливаемая в бортовом накопителе информация, программно-математического обеспечение, реализующее диагностические алгоритмы.
На стадии проектирования ЛА принципы Т. д. осуществляются путём реализации требований к контролепригодности, включая выбор диагностических средств и параметров. При испытаниях авиационной техники оценивается эффективность диагностических средств для заданных условий и режимов полёта. При техническом обслуживании ЛА в процессе эксплуатации авиационной техники используются созданные диагностические средства и на основе анализа полученной информации определяется фактическое техническое состояние ЛА.
Применение Т. д. способствует повышению безопасности и эффективности полётов, снижению трудозатрат на техническое обслуживание и переходу к эксплуатации ЛА по фактическому состоянию.
Авиация: Энциклопедия. — М.: Большая Российская Энциклопедия. Главный редактор Г.П. Свищев. 1994.
.
- техника безопасности
- технология
Смотреть что такое «техническая диагностика» в других словарях:
Техническая диагностика — научная дисциплина, выявляющая причины возникновения отказов и повреждений, разрабатывающая методы их обнаружения и оценки. Цель диагностики разработка способов и средств оценки технического состояния сооружений. Источник … Словарь-справочник терминов нормативно-технической документации
Техническая диагностика — Техническая диагностика область знаний, включающая в себя сведения о методах и средствах оценки технического состояния машин, механизмов, оборудования, конструкций и других технических объектов. Содержание 1 Задачи технического… … Википедия
техническая диагностика — диагностика Область знаний, охватывающая теорию, методы и средства определения технического состояния объектов. [ГОСТ 20911 89 ] [ПБ 12 529 03 Правила безопасности систем газораспределения и газопотребления, утверждены постановлением… … Справочник технического переводчика
ТЕХНИЧЕСКАЯ ДИАГНОСТИКА — установление и изучение признаков, характеризующих наличие дефектов в машинах, устройствах, их узлах, элементах и т. д., для предсказания возможных отклонений в режимах их работы (или состояниях), а также разработка методов и средств обнаружения… … Большой Энциклопедический словарь
Техническая диагностика — отрасль знаний, исследующая техническое состояние объектов (изделий и их составных частей) для установления признаков, обнаружения и поиска отклонений их параметров от допустимых пределов. Техническая диагностика позволяет устранять… … Морской словарь
Техническая диагностика — см. Диагностика техническая … Российская энциклопедия по охране труда
Техническая диагностика — установление, изучение и измерение параметров состояния технических систем в штатных и аварийных ситуациях для обеспечения заданных условий их функционирования, а также для предсказания и предотвращения аварий и катастроф. При штатных режимах… … Словарь черезвычайных ситуаций
Техническая диагностика — научная дисциплина, выявляющая причины возникновения отказов и повреждений, разрабатывающая методы их обнаружения и оценки. Цель диагностики разработка способов и средств оценки технического состояния зданий и сооружений… Источник: ТРЕБОВАНИЯ К … Официальная терминология
техническая диагностика — установление и изучение признаков, характеризующих наличие дефектов в машинах, устройствах, их узлах, элементах и т. д., для предсказания возможных отклонений в режимах их работы (или состояниях), а также разработка методов и средств обнаружения… … Энциклопедический словарь
техническая диагностика — [diagnostics] научно техническая дисциплина, изучающая и устанавливающая признаки дефектов технических объектов, а также методы и средства обнаружения и поиска дефектов. Основной предмет технической диагностики организация эффективной проверки… … Энциклопедический словарь по металлургии
Книги
- Техническая диагностика, В. С. Малкин, Приведены общие представления о диагностике и технических средствах ее реализации, принципах работы измерительных устройств и способах контроля диагностическихпараметров. Дано обоснование… Серия: Учебники для вузов. Специальная литература Издатель: Лань, Подробнее Купить за 980 руб
- Техническая диагностика, Биргер И.А., Книга посвящена теоретическим основам технической диагностики. В ней изложены статистические методы распознавания и разделения в пространстве признаков, метрические и логические методы… Серия: Классика инженерной мысли: машиностроение Издатель: URSS, Производитель: URSS, Подробнее Купить за 979 грн (только Украина)
- Техническая диагностика, Биргер И., Книга посвящена теоретическим основам технической диагностики. В ней изложены статистические методы распознавания и разделения в пространстве признаков, метрические и логические методы… Подробнее Купить за 777 руб
dic.academic.ru
5. Методы оценки технического состояния оборудования – Ассоциация EAM
материал предоставил СИДОРОВ Александр Владимирович
5.1. Общее понятие об оценке технического состояния оборудования
Техническое состояние – состояние оборудования, которое характеризуется в определенный момент времени при определённых условиях внешней среды значениями параметров, установленных регламентирующей документацией [1].
Контроль технического состояния – проверка соответствия значений параметров оборудования требованиям, установленным документацией, и определение на этой основе одного из заданных видов ТС в данный момент времени.
В зависимости от необходимости проведения ТОиР различают следующие виды ТС [2]:
- хорошее – ТОиР не требуются;
- удовлетворительное – ТОиР осуществляются в соответствии с планом;
- плохое – проводятся внеочередные работы по ТОиР;
- аварийное – требуется немедленная остановка и ремонт.
С целью установления фактического ТС оборудования, выявления дефектов, неисправностей, других отклонений, которые могут привести к отказам, а также для планирования проведения и уточнения сроков и объёмов работ по ТОиР проводятся технические обследования (осмотры, освидетельствования, диагностирование). Технические обследования оборудования, эксплуатация которого регламентируется нормативными актами, проводится в порядке, установленном соответствующими нормативными актами.
Технический осмотр – мероприятие, выполняемое с целью наблюдения за ТС оборудования.
Техническое освидетельствование – наружный и внутренний осмотр оборудования, испытания, проводимые в срок и в объёмах, в соответствии с требованиями документации, в том числе нормативных актов, с целью определения его ТС и возможности дальнейшей эксплуатации.
Техническое диагностирование – комплекс операций или операция по установлению наличия дефектов и неисправностей оборудования, а также по определению причин их появления.
5.2. Методы оценки технического состояния оборудования
Различают субъективные и объективные методы оценки ТС оборудования.
Под субъективными (органолептическими) методами подразумеваются такие методы оценки ТС оборудования, при которых для сбора информации используются органы чувств человека, а также простейшие устройства и приспособления, предназначенные для увеличения чувствительности в рамках диапазонов, свойственных органам чувств человека. При этом для анализа собранной информации используется аналитико-мыслительный аппарат человека, базирующийся на полученных знаниях и имеющемся опыте. К субъективным методам оценки ТС относят визуальный осмотр, контроль температуры, анализ шумов и другие методы.
Под объективными (приборными) методами подразумеваются такие методы оценки ТС, при которых для сбора и анализа информации используются специализированные устройства и приборы, электронно-вычислительная техника, а также соответствующее программное и норма-тивное обеспечение. К объективным методам оценки ТС относятся вибрационная диагностика, методы неразрушающего контроля (магнитный, электрический, вихретоковый, радиоволновой, тепловой, оптический, радиационный, ультразвуковой, контроль проникающими веществами) и другие.
5.3. Порядок и особенности проведения визуального осмотра оборудования
Порядок проведения осмотров оборудования основывается на последовательном обследовании его элементов по кинематической цепи их нагружения, начиная от привода до исполнительного элемента. Для этого необходимо знать конструкцию оборудования, состав и взаимодействие его элементов.
Вначале проводится общий осмотр оборудования и окружающих его объектов. При общем осмотре изучается картина состояния оборудования. Общий осмотр может носить самостоятельный характер и применяется при периодических осмотрах оборудования технологическим персоналом.
Под детальным понимается тщательный осмотр конкретных элементов оборудования. Детальный осмотр в зависимости от требований соответствующих нормативных и методических документов, проводится в определённом объёме и порядке. Во всех случаях детальному осмотру должен предшествовать общий осмотр.
Общий и детальный осмотр могут проводиться при статическом и динамическом режиме оборудования. При статическом режиме элементы оборудования осматриваются в неподвижном состоянии. Осмотр оборудования при динамическом режиме проводится на рабочей нагрузке, холостом ходу и при тестовых нагружениях (испытаниях).
Осмотр оборудования при включении или остановке механизма ориентируется в основном на контроль качества затяжки резьбовых соединений, отсутствие трещин корпусных деталей, целостность соединительных элементов. В рабочем режиме дополнительно проверяются биения валов, муфт, утечки смазочного материала, отсутствие контакта подвижных и неподвижных деталей.
При осмотре могут быть применены три основных способа: концентрический, эксцентрический, фронтальный. При концентрическом способе (рисунок 5.1) осмотр ведётся по спирали от периферии элемента к его центру, под которым обычно понимается средняя условно выбранная точка. При эксцентрическом способе (рисунок 5.2) осмотр ведётся от центра элемента к его периферии (по развёртывающейся спирали). При фронтальном способе (рисунок 5.3) осмотр ведётся в виде линейного перемещения взгляда по площади элемента от одной его границы к другой.
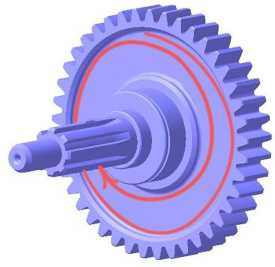
Рисунок 5.1 – Концентрический способ осмотра детали
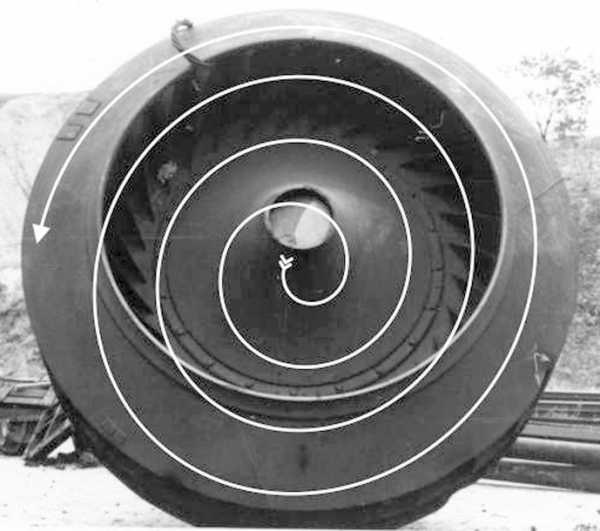
Рисунок 5.2 – Эксцентрический способ осмотра детали
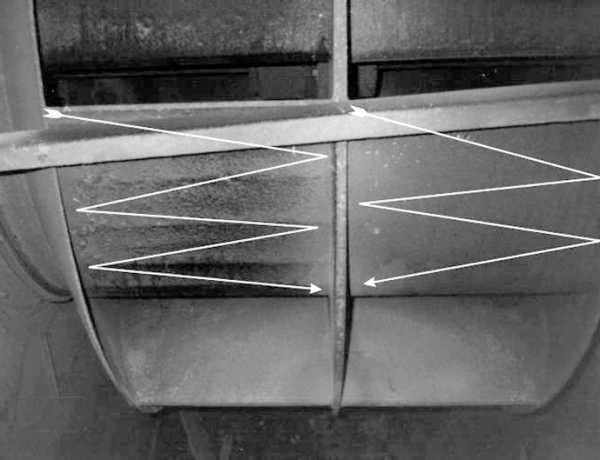
Рисунок 5.3 – Фронтальный способ осмотра детали
При выборе способа осмотра учитываются конкретные обстоятельства. Так, осмотр помещения, где установлено оборудование, рекомендуется проводить от входа концентрическим способом. Осмотр элементов круглой формы целесообразно вести от центра к периферии (эксцентрическим способом). Фронтальный осмотр лучше применять, когда осматриваемая площадь обширна и её можно разделить на полосы.
Под идентификацией дефектов и повреждений подразумевается отнесение неисправностей к определённому классу или виду (усталость, износ, деформация, фреттинг-коррозия и т.п.). Идентифицируя дефект или повреждение, зная его природу, специалист в дальнейшем может определить причины появления неисправности и степень её влияния на ТС оборудования. Идентификация выявленных дефектов и повреждений осуществляется путём сравнения их характерных признаков с известными образцами или описаниями, которые для удобства пользования могут собираться и систематизироваться в иллюстрированных каталогах (таблица 5.1).
Таблица 5.1 – Пример каталога (базы данных) описаний неисправностей, дефектов и повреждений
Внешний вид повреждения | Описание повреждения | Причины возникновения |
---|---|---|
Осповидное выкрашивание ролика подшипника |
| |
Угловое смещение пятна контакта зубчатой передачи |
| |
![]() | Хрупкое разрушение металла втулки зубчатой муфты |
|
Завершающая стадия заключается в дополнительном осмотре элементов оборудования для уточнения ранее полученных результатов и их регистрации в отчётных формах.
Регистрационные формы – это определённый порядок записи результатов опроса, собственно осмотра и дополняющие их графические изображения деталей и объекта в целом: рисунки, эскизы, чертежи, фотоснимки и т.п. На графических изображениях должны обозначаться точка начала осмотра и его направление, места расположения обнаруженных дефектов и повреждений.
Формализация результатов проведения осмотра осуществляется протоколом осмотра. В протоколе осмотра отражается то, что специалист имел возможным обнаружить при осмотре, в том виде, в котором обнаруженное наблюдалось. Выводы, заключения, предположения специалиста о причинах возникновения дефектов и повреждений остаются за рамками протокола и обычно оформляются отдельным актом или отчётом. Не заносятся в протокол и сообщения лиц о ранее обнаруженных отклонениях, а также произошедших до прибытия специалиста изменениях обстановки. Такие сообщения оформляются самостоятельными протоколами.
К составлению протокола осмотра надо подходить с учётом того, что он может выступать в качестве самостоятельного документа. В этих целях протокол составляется краткими фразами, дающими точное и ясное описание осматриваемых объектов. В протоколе употребляются общепринятые выражения и термины, одинаковые объекты обозначаются одним и тем же термином на протяжении всего протокола. Описание каждого объекта осмотра идёт от общего к частному (вначале даётся общая характеристика осматриваемого оборудования, его расположение на месте осмотра, а затем описывается состояние и частные признаки). Полнота описания объекта определяется предполагаемой значимостью и возможностью сохранения данных. Фиксируются все имеющиеся признаки дефектов и особенно те, которые могут быть со временем утрачены. Каждый последующий объект описывается после полного завершения описания предыдущего. Объекты, связанные между собой, описываются последовательно с тем, чтобы дать более точное представление об их взаимосвязи. Количественные величины указываются в общепринятых метрологических величинах. Не допускается употребление не-определённых величин («вблизи», «в стороне», «около», «рядом», «почти», «недалеко» и пр.). В протоколе отмечается факт обнаружения каждого из следов и предметов, в отношении каждого объекта указывается, что было с ним сделано, какие средства, приёмы, способы были применены. При описании оборудования и отдельных его элементов в протоколе приводятся ссылки на планы, схемы, чертежи, эскизы и фотографии. Каждый осматриваемый элемент оборудования должен иметь отдельную запись о результатах его осмотра. Выводы протокола должны содержать информацию о наличии и характере дефектов, а при невозможности его установления – о необходимости последующего проведения идентификации. [3]
Перечень ссылок
- Словарь терминов и определений // Консалтинговый проект “EAM”. – https://eam.su/slovar-terminov-i-opredelenij.html.
- Механическое оборудование: техническое обслуживание и ремонт / В.И. Бобровицкий, В.А. Сидоров. – Донецк: Юго-Восток, 2011. – 238 с.
- Зданевич В., Сидоров В.А. Осмотр механического оборудования как метод технической диагностики // Техническое Обслуживание и Ремонт, 2010. – №4. – С. 12-18.
Вопросы для контроля
- Какие виды ТС выделяют в зависимости от необходимости проведения ТОиР?
- В чём заключается отличие между объективными и субъективными методами оценки ТС?
- Опишите порядок проведения визуального осмотра оборудования.
eam.su
Средства диагностики технического состояния оборудования
Средства диагностики технического состояния оборудования служат для фиксирования и измерения величины диагностических признаков (параметров). Для этого применяют приборы, приспособления и стенды сообразно характеру диагностических признаков и методам диагностики.
Значительное место среди них занимают электроизмерительные приборы (вольтметры, амперметры, осциллографы и др.). Они широко применяются как для непосредственного измерения электрических величин (например, при диагностике систем зажигания и электрооборудования автомобиля), так и для измерения неэлектрических процессов (колебаний, нагрева, давления), преобразованных при помощи соответствующих датчиков в электрические величины.
При диагностике механизмов наиболее часто используют: датчики сопротивления, концевые, индукционные, оптические и фотоэлектрические датчики, при помощи которых можно измерять зазоры, люфты, относительные перемещения, скорость и частоту вращения проверяемых деталей; термосопротивления, термопары и биметаллические пластины для измерения теплового состояния деталей; пьезоэлектрические и тензометрические датчики для замера колебательных процессов давления, биений, деформаций и др.
Одно из положительных качеств электроизмерительных приборов — удобство получения информации, а также в перспективе возможность ее анализа при помощи ЭВМ.
В зависимости от полноты и степени механизации технологических процессов диагностику можно проводить выборочно, только для контроля технического состояния отдельных сборочных единиц, или комплексно для проверки сложных агрегатов, таких как двигатель, и, наконец, комплексно для диагностики машины в целом.
В первом случае используются для отдельных измерений такие диагностические приборы как стетоскопы, манометры, тахометры, вольтметры, амперметры, секундомеры, термометры и другие переносные приборы. Во втором случае приборы комбинируют в виде передвижных стендов, в третьем случае — ими комплектуют пульты управления стационарных стендов.
Передвижным комплексным средством диагностики является ходовая диагностическая станция. Она может обеспечивать диагностику технического состояния автомобилей в местах их временного размещения. Компоновка ходовой диагностической станции возможна на базе прицепа достаточно большой грузоподъемности.
Основными требованиями к средствам диагностики являются: обеспечение достаточной точности замеров, удобство и простота использования при минимальной затрате времени.
Помимо различных приборов, индикаторов узкого назначения в систему диагностических средств включают комплексы электронной аппаратуры. Эти комплексы могут состоять из датчиков — органов восприятия диагностических признаков, блоков измерительных приборов, блоков обработки информации в соответствии с заданными алгоритмами и, наконец, блоков хранения и выдачи информации в виде запоминающих устройств для преобразования информации в удобный для использования вид.
Методы и средства диагностического контроля насосных агрегатов
Диагностический контроль насосных агрегатов осуществляется по параметрическим и виброакустическим критериям, а также по техническому состоянию отдельных сборочных единиц и деталей, оцениваемому при выводе насосов из эксплуатации.
Для проведения диагностических контролей используется виброаппаратура с возможностью измерения спектральных составляющих вибрации, шумомеры с возможностью измерения октавных составляющих, приборы, позволяющие определять техническое состояние подшипников качения или аналогичные им, но с большими функциональными возможностями отечественного или зарубежного производства.
Средства контроля вибрации и методы вибродиагностики должны обеспечивать решение следующих задач:
своевременного обнаружения возникающих дефектов составных частей оборудования и предотвращения его аварийных отказов;
определения объема ремонтных работ и рационального их планирования;
корректировки значений межремонтных интервалов и прогнозирования остаточного ресурса составных частей оборудования по его фактическому техническому состоянию;
проверки работоспособности оборудования после монтажа, модернизации и ремонта, определения оптимальных режимов работы оборудования.
Насосные агрегаты должны быть оснащены контрольно-сигнальной виброаппаратурой (КСА) с возможностью контроля текущих параметров вибрации, автоматической предупредительной сигнализацией и автоматическим отключением при предельно допустимом значении вибрации.
До установки контрольно-сигнальных средств контроль и измерение вибрации осуществляются портативными (переносными) средствами виброметрии. Датчики виброаппаратуры устанавливаются на каждой подшипниковой опоре.
В качестве измеряемого и нормируемого параметра вибрации устанавливается среднее квадратическое значение (СКЗ) виброскорости в рабочей полосе частот 10-1000 Гц.
Измерение значений виброскорости осуществляется в вертикальном направлении на каждой подшипниковой опоре. При этом регистрируется соответствующий режим работы насоса — подача и давление на входе.
В табл. 7.3 приведены допустимые уровни вибрации при эксплуатации центробежных насосов.
Таблица 7.3 Предельно допустимые нормы вибрации при эксплуатации насосов
Высота оси вращения ротора, мм | Среднее квадратическое значение виброскорости, мм/с |
До 80 80-132 132-225 Свыше 225 | 1,8 2,8 4,5 7,1 |
У насосов, не имеющих выносных подшипниковых опор (насосы со встроенными подшипниками), вибрация измеряется как можно ближе к оси вращения ротора.
При определении шумовых характеристик измеряются в соответствии с ГОСТ 23941 уровень звука LА (в дБА) в контрольных точках; уровень звукового давления Li, (в дБА) в октавных полосах частот (от 31,5 до 8000 Гц) в контрольных точках.
Приборы, применяемые для измерения шумовых характеристик, число точек измерения и измерительные расстояния определяются ГОСТ 12.1.028, технической документацией на конкретный шумомер и условиями эксплуатации диагностируемого оборудования. При определении шумовых характеристик (базовых и текущих) должны соблюдаться одинаковые условия измерений (режим работы, количество одновременно работающего оборудования и др.).
По результатам диагностических контролей принимается решение о выводе насосов в ремонт или их дальнейшего использования по назначению.
В табл. 7.4 приведены виды диагностических работ и допустимые значения контролируемых параметров для магистральных и подпорных насосов нефтеперекачивающих станций.
Периодичность, форма и объем регистрируемых параметров должны быть определены нормативными документами с учетом возможной ручной, автоматизированной или смешанной системы регистрации информации.
Основные причины вибраций насосных агрегатов и характер их проявления представлены в табл. 7.5.
Основные причины вибрации насосных агрегатов обусловливаются механическими, электромагнитными и гидродинамическими явлениями, а также жесткостью опорных систем.
Таблица 7.4
Виды диагностических работ и допустимые значения
контролируемых виброакустических параметров и значений
температур для магистральных и подпорных насосов
Вид диагностических работ | Контролируемый параметр и место измерения | Допустимое значение параметра |
Оперативный диагностический контроль Плановый диагностический контроль Неплановый диагностический контроль Послеремон-тный диагностический контроль | СКЗ виброскорости на подшипниковых опорах в вертикальном направлении СКЗ виброскорости на лапах корпуса насоса в вертикальном направлении Температура подшипников СКЗ и спектральные составляющие виброскорости на всех подшипниковых опорах в трех взаимно перпендикулярных направлениях СКЗ виброскорости на лапах корпуса насоса, головках анкерных болтов в вертикальном направлении Уровень шума Температура подшипников Вибрации опорно-упорного подшипника или подшипников качения Контролируемые параметры, их допустимые значения и место измерения соответствуют плановому диагностическому контролю СКЗ виброскорости на подшипниковых опорах в трех взаимно перпендикулярных направлениях СКЗ виброскорости на лапах корпуса насоса и головках анкерных болтов в вертикальном направлении Вибрация опорно-упорного подшипника или подшипников качения Температура подшипников | 6,0 мм/с 1,8 мм/с Увеличение температуры относительно базового значения на 10 °С 6,0 мм/с 1,8 мм/с Увеличение относительно базового значения на 6 дБА Увеличение температуры относительно базового значения на 10°С Не более 45 дБ Не более 4,5 мм/с Не более 1 мм/с Не более 35 дБ Не выше 70°С |
Таблица 7.5 Влияние неисправностей на виброакустический спектр насосных агрегатов
Причина повышенной вибрации | Направление | Причина повышенной вибрации | Направление |
Дисбаланс вращающихся элементов. Ослабление посадки деталей ротора1 Несоосность2 Нецилиндричность шейки вала Повреждение подшипников качения Овальность внутреннего кольца Радиальный зазор Неуравновешенность, разностенность сепаратора Волнистость, гранность шариков Дефекты дорожки внутреннего кольца Дефекты дорожки внешнего кольца | Радиальное Радиальное и осевое Радиальное Радиальное и осе вое, обычное с низкой амплитудой | Неравномерный зазор ротор-статор электродвигателя Короткое замыкание обмотки возбуждения синхронного электродвигателя «Масляное биение» в подшипнике скольжения Неравномерность потока охлаждающего воздуха Гидравлический небаланс рабочего колеса Неравномерность поля скоростей и вихреобразование в насосе Кавитационные явления в насосе Неисправность зубчатой муфты3 Ослабление жесткости подшипникового узла | Радиальное Радиальное Радиальное Радиальное Радиальное Радиальное Радиальное, осевое Радиальное, горизонтальное |
1 Частая причина высокой вибрации оборудования. 2 Частая причина вибрации. Осевая вибрация — главный показатель, часто она превышает радиальную. 3 Для обеих смежных с муфтой подшипниковых опор. |
При проведении измерений необходимо попытаться разделить перечисленные источники повышенной вибрации насосных агрегатов. При наличии повышенной вибрации подшипниковых опор агрегата необходимо проверить жесткость крепления подшипниковых опор к корпусу или раме, жесткость крепления корпуса насоса и рамы двигателя к фундаменту. Повышенная вибрация в горизонтальной плоскости указывает на уменьшение жесткости в горизонтальных направлениях.
По результатам измерения вибрации для каждой контролируемой точки строится график изменения среднего квадратического значения виброскорости в зависимости от наработки (рис. 7.7). До виброскорости 6,0 мм/с график можно представить прямой линией, проведенной согласно полученным значениям вибрации. Далее график строится по значениям вибрации, соответствующим наработке насосного агрегата после виброскорости 6,0 мм/с. График, построенный после достижения уровня вибрации 6,0 мм/с, как правило, будет располагаться под большим углом к оси абсцисс и позволит оценить время наступления предельно допустимого значения вибрации τ1 при предельном значении виброскорости 7,1 мм/с или τ2 — при 11,2 мм/с.
Для более достоверной оценки технического состояния и остаточного ресурса отдельных деталей или узлов рекомендуется строить также график по основным спектральным составляющим, указывающим возможные дефекты насосных агрегатов.
В процессе эксплуатации насосного агрегата его техническое состояние меняется из-за износа деталей и узлов. Наиболее распространенной и значимой причиной ухудшения характеристик насоса в процессе эксплуатации является износ деталей щелевого уплотнения рабочего колеса.
Насосные агрегаты необходимо выводить в ремонт при снижении величины напора насоса от базовых значений на 5-7 %.
Значение возможного снижения КПД относительно базового значения может уточняться для конкретного типоразмера насоса на основании экономической оценки из условия, что стоимость ремонта, при котором обеспечивается восстановление первоначального КПД, будет выше затрат, вызванных перерасходом электроэнергии из-за снижения КПД насоса.
Диагностирование состояния насосных агрегатов по параметрическим критериям допускается проводить как на основе данных, полученных по каналам телемеханики, так и на основе контрольных измерений с применением образцовых средств измерений давления, подачи, мощности, частоты вращения ротора насоса, плотности и вязкости перекачиваемой жидкости.
Измеряемые параметры и средства измерения:
давление на входе и выходе насосного агрегата измеряется штатными первичными преобразователями давления с точностью 0,6 % при использовании АСУ или образцовыми манометрами класса 0,25 или 0,4;
подача определяется по узлу учета, по объемам резервуаров с помощью переносных ультразвуковых расходомеров или другими способами;
мощность, потребляемая насосом, измеряется при помощи штатных первичных преобразователей мощности с точностью не ниже 0,6 %. При установившихся режимах для грубой оценки допускается определять мощность по счетчику потребляемой электроэнергии или вольтметру и амперметру;
частота вращения ротора замеряется датчиком частоты вращения с точностью 0,5 %;
плотность и вязкость перекачиваемой жидкости определяются по узлам учета или в химлаборатории.
Замер параметров проводится только при установившемся (стационарном) режиме перекачки.
Контроль стационарности режима осуществляется по подаче (при возможности непосредственного измерения) или по давлению на входе или выходе насосного агрегата. Колебания контролируемого параметра не должны превышать ± 3% от среднего значения.
Параметры измеряются при бескавитационном режиме работы насосного агрегата (контролируются при измерении вибрации и по давлению на входе в насос).
studfiles.net
Диагностика оборудования | СервисТЕХ
Описание
В наше время диагностика станков с ЧПУ — самый сложный процесс в поиске неисправности и последующего его устранения.
Многообразие технических решений и стандартов исполнения, реализованных на уровне электроники со стороны ведущих производителей и конструктивных компонентов механических узлов станкостроителя усложняют диагностику, и влияют на время реакции при проведении диагностики, усложняя процесс в поиске текущей неисправности с последующим его устранением или ремонтом.
Технически диагностика представляет собой универсальный подход в определённом комплексе работ, характеризуя диагностику как направление на установление и анализ признаков неисправностей, давая оценку состояния различных систем управления при выявление проблем, а также формирования путей их решения.
Надёжность оборудования выражена в безотказной работе и высокой точности обработки. Но она имеет свой ограниченный срок работоспособности. Это связанно не только с износом оборудования за весь период работы до капитального ремонта. На первых этапах диагностики необходимо выявить системные проблемы, обусловленные характером взаимодействия смежных узлов, с учётом уникальности конструктивных особенностей оборудования при различной структуре их взаимодействия между собой. Оперативный анализ изучения поведения оборудования в целом, системное отклонение технологического процесса и периодические сбои электроники необходимо проверять на первоначальной стадии диагностического исследования.
Основным требованием к диагностике является определение причин возникновения аварии, произошедшей в системе и отклонений ее параметров от норм и допусков оборудования как следствие. В основном неисправности и их причины не всегда и не обязательно совпадают с учётом изменяющегося технического состояния оборудования. При общем характере поведения различного типа современного оборудования необходимо проводить причинно-следственный анализ. Данный анализ может указывать на этапы возникновения нарушений во временной составляющей процессов подводящих к серьёзным последствиям аварии.
Исследование причин нарушений нормального состояния системы управления при различных способах решения возникающих проблем, которые привлекают внимание при изучении причин нарушений работоспособности оборудования, является необходимым условием результативности диагностического исследования, определяя влияние текущих причин.
Диагностика станков с ЧПУ позволяет решить следующее:
- определить состояние системы управления и подчинённых устройств в замкнутом контуре управления с учетом смежных по контролю различных подчинённых потоков управления;
- определение зависимости выхода компонентов и узлов оборудования «причина-следствие», более раннее определение выхода из строя узлов и компонентов управления;
- при системном характере поведения причин сбоя оборудования, определение нарушений взаимодействия компонентов управления;
- статистика причин, вызывающих нарушения в системе управления и принятие решений для исключения нарушений работы оборудования;
- учесть и исследовать из множества причин, влияющих на нарушения работоспособности оборудования, и принять наиболее правильные решения для последующего их исключения;
- определить возможные альтернативные варианты решения в направлении восстановления, исходя из сложившейся структуры взаимодействия элементов системы управления;
- при принятии решений оценить возможные последствия с точки зрения эффективности при восстановлении работоспособности в целом;
- выделение ключевых проблем и основных причин, вызывающих проблемную ситуацию на оборудовании
Оборудование
Для проведения исследований, определения технических параметров применяется Оборудование
Виды работ
Для определения стоимости диагностики, вы можете указать работы из списка в соответствии с примером:
Загрузить перечень работ по Диагностике
- Выезд специалиста с использованием мерительного инструмента;
- Выезд специалиста с использованием телескопической измерительной система Ballbar Renishaw;
- Выезд специалиста с использованием с использованием интерферометра.
Длительность работ:
- Диагностика механических узлов — от 1 дня и более, в зависимости от задачи;
- Диагностика ЧПУ — от 2 дней и более, в зависимости от задачи.
Стоимость
С ценами на услуги можно ознакомиться в разделе Стоимость услуг
Образец договора
По ссылке представлен образец договора на проведение диагностических работ
Комплексный отчет
По желанию заказчика по окончанию диагностических работ может быть составлен Комплексный отчет по проведенным работам
servicetex.ru