Доработка ГБЦ классики
Проблема кроется в стыках ГБЦ с впускным и выпускным коллекторами. «Ступеньки»могут достигать до 5 мм.Представьте какая преграда на пути воздушного потока,движущегося почти со скоростью звука. Что нужно(без набора ключей для снятия и разборки ГБЦ)
1) Небольшая электродрель
2) Борфреза(лучше разных форм и твёрдосплавные)
3) Шарошка из абразивного материала
4) Стеpжень (или тpубка) для шлифовки — диаметp 5-6 мм, длина 150-180 мм,
с одной стоpоны нужно сделать пpодольную пpоpезь ножовочным полотном
на длину 20-25 мм.
5) Наждачная бумага помельче(но не нулёвка)
6) Круглый напильный(побольше)с мелкой насечкой
7) Острая чертилка
8) Пластилин
Снимаем ГБЦ,на класике рекомендую снять капот,а то он будеть мешать, предварительно очертив карандашом или маркером места крепления,чтобы потом не регулировать его.
Процедура снятия/установки ГБЦ подробно расписана в «умной книжке» (руководстве по эксплуатации).
Разбираем головку,может понадобиться съёмник для клапанов(желательно), хотя можно воспользоваться и подручными средствами.
Закрепляем её на столе или другом удобном месте,по старой прокладке отчерчиваем границы впускных и выпускных каналов.Вообще их хорошо видно на бывшей в работе головке,там остаются следы нагара.А ещё точнее можно сделать с помощью пластилина,разогрейте его руками,облепите каналы головки вокруг,смочите водой коллектор и прижимите посильнее, выдавленный пластилин убираете,и сразу становиться видно в какую сторону расстачивать.После чего потихоньку,аккуратно доводим стыки каналов.
Движения проводите по дуге,не останавливаясь на месте,чтобы не было зарезов,и медленно перемещаетесь в глубь каналов,выводите форму канала так,чтобы небыло резких закруглений,горбов и «ступенек»,по возможности, радиуса внутри каналов должны быть как можно больше.
Правильность формы проверяйте проводя пальцем,как можно чаще,лучше недорезать, чем перерезать.
Следующий шаг нашей доработки ГБЦ: проверка сопряжений каналов с сёдлами клапанов,тут тоже бывают ступеньки,убираем их.Делайте это очень аккуратно,чтобы не повредить фаску седла клапана.Со стороны камер сгорания тоже неплохо бы сделать скругления в каналах,только осторожнее (потребуется выпрессовка направляющих втулок клапанов).
Теперь берём трубку(стержень)с прорезью на конце,в прорезь вставляем наждачку и обматываем вокруг стержня,и начинаем шлифовку каналов ГБЦ. Пришла очередь впускного и выпускного коллекторов,с ними поступаем аналогично ГБЦ.
На фото видны места
обработки(красным пунктиром).
Точность контролируем
пластилином,как было описано
выше.Каналы в коллекторе
нужно сделать вровень с
каналами в ГБЦ,или чуть
поменьше,чтобы поступающая
смесь не нашла себе преград.
Так же как и ГБЦ шлифуем впускной коллектор. Теперь круглым напильником стачиваем лишнюю сварку внутри каналов приёмной трубы(штанов),где приварен фланец к трубам,шов может выступать на 5 мм по окружности.
Проще приёмную трубу снять с машины,так будет намного удобней.
Перед сборкой тщательно промойте и продуйте детали от стружки и абразивной пыли,и обязательно смажте маслом стальные детали,купите новые прокладки и проверьте их на соосность каналов,при необходимости подрежте.
Собираем и устанавливаем на место,не забудьте старую прокладку ГБЦ и блока, сменить на новую.
После этой операции я был приятно удивлён, когда на своей «семёрке» при разгоне легко поднял стрелку до 5500 об/мин,даже чуть-чуть перевалил,такого раньше не было,она разгонялась не охотно.
Если вам этого мало, но есть терпение и время,и самое главное желание…можно увеличить диаметры каналов,это даст уже ощутимую прибавку к мощности и оборотам.
Нам понадобиться большое сверло,какое только влезет в патрон дрели,обычно больше 9мм не лезет,то есть 8-9 мм,желательно подлиннее.
Ветошь и наждачка:грубая,средняя и мелкая.
Два длинных болта,один можно гнутый,или придётся погнуть чуть-чуть.
Две шайбы диаметром на 1 мм меньше расчётного диаиметра каналов, для контроля диаметра каналов,впускные растачивают до 34мм,выпускные до 30,больше опасно.
Вот примерно,что нужно:
Наматываем на сврло ветошь
с грубой шкуркой,чтобы плотно
входило в канал, и аккуратно
расстачиваем,начинать лучше с
коллектора.При этом
контролируйте толщину стенок.
Вот такая разница получается:
Контроль производят вот так:
Шайбы должны проходить
свободно,параллельно оси
канала.
Впускной коллектор,больше чем на 2/3 длины расточить сложно,оставшуюся перегородку убирают при помощи сверла.
Следующий этап-шлифовка,
то есть обрабатываем более
мелкой шкуркой,а потом совсем
мелкой(но не нулёвкой), не
переусердствуйте.
Теперь ГБЦ.
Со стороны коллектора в ней можно,как уже говорилось,сделать диаметр немного больше.Протачиваем до направляющех втулок(их лучше выпрессовывать,что бы не повредить),потом начинаем обрабатывать со стороны камер сгорания,осторожнее с сёдлами клапанов.
Хорошо видно, как убирается нарост вокруг отверстия под направляющую втулку, который очень неслабо закрывает канал:
После обработки всё промывается и сушиться.
Итог:
Впуск: коллектор 34 (было 29), каналы ГБЦ 34 (было 29),у седла 33.5 (было 32.5)
Выпуск: каналы у седла 28 (было 27, наполовину перекрыты выступом под направляющую), на выходе из ГБЦ 30 (было 27), коллектор 30(было 29), седла 28 (были 27.5).
Результаты — в головке глядя на вход в канале, можно увидеть выход, в недоработанной такого нет:
Теперь насчет направляющих. Тщательно взвесив все за и против, решил остановиться на своем варианте и пилить ее сложно-пространственно.
Для начала разметил на ней метчиком линию, по которой она торчит в канале, также по всему периметру (чтоб легко точить и потом запрессовывать) прочертил ее перед и зад.
Смысл был в том, чтобы
максимально снять
торчащего металла, и в
то же время оставить по
максимуму по площади
канала изнутри (масло) и
не трогать вообще ее
нагруженную сторону
(разобъет), и при этом все
максимально аэродинамично
сгладить.
Впускные получились по
оконцовке такими:
Как видно, на пятке (та сторона, на которую давит при работе клапан) я практически не трогал металл, поэтому вряд-ли деформируется.
С выпускными немного тяжелее — там и отвод тепла и нагруженность сильнее, и направление потока больше. Поэтому смысл такой-же, но объем работ значительно меньше:
Вот так торчит стандартная в обработанном впускном канале:
А это доработанная
Доработка клапана…
Тяжеловато было, резец очень плохо берет, даже твердосплавный… Новый выпускной клапан практически вообще не берется, мне советовали на доработку брать только б/у, они лучше точатся — материал мягче.
Зато потом зажал в дрель и доводил форму шкуркой — берется на ура! Медленно,зато уверенно снимается металл.
Вот что получилось в итоге:
обработанная фотка стокового впускного клапана, красным — снятый металл). Запрессовал направляющие изготовленной оправкой (стальной прут, внутри отв. 11.0мм) ГБЦ в духовке до 100 град, направляющие в морозилку.
Забивать надо аккуратно, но очень быстро. Не забыть снять шпильки распредвала, они будут мешаться (без снятия крайних вообще не запрессовать). Сначала лезет легко потом нагреваются, но все равно лезут нормально. Выбивались, чесслово, с гораздо большим усилием. Главное, шустрее орудовать.
Если все мои изыскания сжать в единый временной промежуток и выбросить эстетику (вроде надраивания до блеска головки), то в 5 рабочих дней уложиться можно легко.
Дерзайте!!!
Читайте также Облегчение и балансировка маховика
Некоторые материалы использовались с сайта www.vaz.ee
LADATUNING.NET
www.ladatuning.net
Фрезеровка Гбц классика | Turbobazar.ru
Зависимость степени сжатия двигателя ВАЗ-21011 от глубины фрезерования головки блокаГлубина фрезерования, мм
0,2
0,5
0,8
1,0
1,2
1,5
1,8
2,0
2,5
2,9
3,2
Степень сжатия
9,0
9,2
9,4
9,5
9,8
9,9
10,2
10,4
11,0
11,5
12
Завод ВАЗ выпустил головки блока с тремя маркировками, отлитыми с левой стороны над плоскостью разъема. Головки с маркировкой 2101-1003015 и 21011-1003015-10 (унифицированная головка, устанавливаемая в настоящее время на двигатели всех моделей) имеют одинаковый объем камеры сгорания- 32 см3. Головка блока с маркировкой 21011-1003015 устанавливалась до середины 1976 г. только на двигатели ВАЗ-21011. Это следует учитывать при комплектации деталей для сборки двигателя.
У двигателя ВАЗ-2106 поршень не доходит до верхней плоскости блока 1,9 мм (у ВАЗ 21011-0,1 мм), поэтому в табл. 30 приведены значения степени сжатия в зависимости от глубины фрезерования не только головки блока, но и самого блока или головки и блока вместе. Фрезерование головки блока более чем на 3 мм опасно с точки зрения вскрытия водяных каналов.
Обе таблицы составлены с учетом заводской комплектации в настоящее время, т. е. имеется в виду установка унифицированной головки на все двигатели. Поршни в двигателях ВАЗ-21011 имеют плоское днище, а поршни ВАЗ-2106-с проточкой на днище (объем этой проточки 1,7 см3).
Лучше всего фрезеровать полностью разобранную головку цилиндров, т. е. без всасывающего и выхлопного патрубков, бензонасоса, распределительного вала и всей системы газораспределения, но с закрепленной крышкой шестерни привода распределительного вала (М-412).
Фрезеровать желательно на вертикально-фрезерном станке фрезой, которая всю плоскость головки по ширине может пройти за один проход. Впрочем, годится любая другая технология фрезерования при условии, что чистота обработки плоскости головки будет не хуже производимой заводом-изготовителем. Как правило, опытный фрезеровщик проходит плоскость головки 2 или 3 раза независимо от выбранной глубины фрезерования. Делается это во избежание ошибок, которые потом трудно исправить. После закрепления головки на станке проверяется правильность ее установки по уровню. Первый проход- проверочный — осуществляется на меньшую глубину, чем предполагаемая для выбранной степени сжатия. Если после первого прохода высота головки цилиндров по всему периметру одинакова (исходный размер стандартной головки-108,5 мм), то можно уверенно производить окончательную обработку.
После фрезерования снимаются заусенцы и головка тщательно очищается от стружки. Желающим произвести подготовку головки блока цилиндров по программе максимум, однако, рано думать о сборке головки и постановке ее на двигатель.
Для двигателей ВАЗ, особенно форсированных до степени сжатия 11,0-11,5, хорошо зарекомендовала себя комбинированная прокладка головки блока, состоящая из колец отожженной красной меди, которые уплотняют камеру сгорания, и стандартной прокладки для уплотнения соединений по системе охлаждения и смазки.
turbobazar.ru
Доработка ГБЦ классики | Блог по доработке,тюнингу и обслуживанию автомобиля и скутера
Для начала расчеты. Тупо площади считаем.
Впускной канал, самая узкая часть — там, где выпирает
направляющая.
(29*29*3,1415/4)-(14*14*3,1415/4) =
660 — 154 = 506 мм2
Щель впускного клапана в максимальном подъеме:
33*3,1415*10 = 1037 мм2
Отсюда видно, что размеры канала значительно уступают
по сравнению с другими узкими местами впускного тракта.
Это действительно только в момент полного открытия
клапана, но это время почти полного открытия
подавляющее. Короче, нада делать.
Максимум (покажу
на фото) — это 34мм, на большее стандартный коллектор не
расточить, стенка 1мм остается.
Считаем с учетом того, что клапанную ножку обточим до
7мм, а направляющую срежем заподлицо:
(34*34*3,1415/4)-(7*7*3,1415/4) = 909 — 39 = 870 мм2
получается, увеличиваем площадь самого узкого места
на 70%, неплохо…
Абсолютные данные не точные, но в сравнении — ценная информация.
От составителя: Двигатель 1300, ГБЦ 2101, система питания – Webber 2101 23х24
Далее голова снимается с машины,
разбирается и моется.
Шикарно конечно моется
углекислотой, но не было огнетушителя под рукой. Мыл
обычным керосином, а потом в ванной щеткой с порошком.
Кстати, нужно не забыть смазать маслом все стальные
детали (направляющие, седла, втулки под рокера), чтоб
ржа не схватила.
Еще неплохой по слухам метод, когда
ВД40 растворяется в незамерзайке. жидкости для омывателя
— получается белая эмульсия, которая все смывает
легко…
Шпильки, кстати, лучше тоже скрутить, но мне покуда не мешали…
Пациент:
Направляющие выбиваются приспособлением, которое я изготовил из болта. Выбиваются легко и непринужденно… наружа приспособы 13.5, внутренний штырь для направления — 8мм.
Теперь все готово для пиления каналов. Я бы советовал начинать с коллектора, поскольку в голове запаса металла по краям больше, лучше подгонять голову под коллектор а не наоборот…
Замеры: каналы в голове 29, выпуск 27, в коллекторе — 29, вып. коллектор 29.
растачивал я шкуркой в дрели. Самая эффективная головка ИМХО — это вал (в моем случае сверло толстое), на который наматывается ветошь, а на нее — полоса шкурки дето в 20см длиной (ессно все внахлест мотается, чтоб не соскакивало)
Использовал я самую грубую шкурку НА
ТРЯПИЧНОЙ ОСНОВЕ какая только была под рукой — это
24-ка. Один канал в голове я ею делал за 2 часа.
Также для удобства сделал наборчик шайб на палочке
(см. фото), номинальной (34мм) и уменьшенного диаметра
(33) и комплект для выпуска. Такими ну очень удобно
контролировать диаметр канала, чтоб не махнуть лишку —
такая шайба должна свободно проходить по каналу
перпендикулярно оси, и не сильно болтаться.
Технология — мотаем ветошь со шкуркой
так, чтобы «головка» еле лезла в дырку, начинаем
сверлить потихоньку пропихивая все дальше, покуда шкурка
не рассыплется. Потом можно кусок оторвать или
перевернуть полоску и заново… Контролируем диаметр
шайбой, новую полосу шкурки и заново поехали…
неплохо бы еще заиметь инструмент для измерения
толщины стенок, но я пользовался пинцетом с налепленными
на концы кусочками пластилина.
Коллектор:
разительно отличаются по
диаметру пропиленные каналы от не пропиленных:
коллектор точится значительно тяжелее чем голова, из-за того, что можно подлезть только с одной стороны (со стороны карба не сильно то и просунешься).
Смог пропилить коллектор до 34-х только
на 2/3, пришлось устранить сверлом перегородку между
каналами:
как было
как стало
Все, шайбы свободно проходят:
Теперь очередь головы.
нужно состыковать каналы коллектора с
головой. Пробовал разные варианты с отпечатками и
проч… сложно все это как-то… Остановился на
пластелине — леплю по окружности на голове, смачиваю
водой коллектор, прижимаю рукой, отпускаю, выдавленный
пластилин внутрь коллектора срезаю — четко видно, куда
нада править голову.
Поправить лучше отдельно перед
расточкой, потому что шкурка раздает во все стороны
одинаково. Поправить можно напильником круглым, я просто
грубо обтесал дырку в нужную сторону, чтобы она
равномерно повторяла контур дыры в коллекторе. Кстати,
лучше выход из головы сделать чуть побольше, например
35, потому что ступенька все равно будет, лучше чтобы
она была не в сторону головы. Но специально расширять не
нада — 35 и так получится от постоянного шныряние
шкуркой через эту дырку.
А потом поехали… Растачиваем
равномерно со стороны коллектора, покуда шайба не будет
пролазить до дырки под направляющую, потом лучше точить
со стороны КС. С этой стороны осторожнее с седлами!!!
Растачиваются они на удивления быстро и легко, можно
полностью уничтожить место под фаску.
разница
очевидна:
Хорошо видно, как убирается нарост вокруг дырки под направляющую, который очень неслабо закрывает канал:
Каналы все пропилены, голова вымыта. Не
забыть все стальные части перед мойкой смазать маслом,
седла клапанов в первую очередь!). Для промывки системы
охлаждения использовал электролит для акку — т.е. серную
кислоту. Перевернул голову вверх тормашками, закупорил
все отверстия и аккуратно, чтоб кислота не попала на
наружную поверхность головы (она все ж алюминий хорошо
ест), заливал внутрь, медленно покачивая голову. Накипь,
налет и ржа растворяется полностью за несколько секунд,
полный цикл возни головы в кислоте не думаю, что нужно
растягивать более чем на 5 минут. Также аккуратно
кислоту сливаем.
На фото отлично виден уровень
стояние кислоты — сверху все грязно, снизу девственно
чистый алюминий:
После голову сразу промыть, можно в растворе соды или стирального порошка и побыстрее высушить. Например, в духовке =)
Итого:
впуск коллектор 34 (было 29), каналы 34
(было 29), седла 33.5 (было 32.5)
выпуск каналы у
седла 28 (было 27, наполовину перекрыты выступом под
направляющую), на выходе из головы 30 (было 27),
коллектор 30(таким и был), седла 28 (были 27.5).
Ушло 0.5 м2 шкурки №24 и гдето столько же ветоши. На канал в впускном коллекторе уходило 2 часа, в голове впуск — 1 час. В голове выпуск — пол часика…
Нарезал небольшие ушки в КС:
Результаты — в голове глядя на вход в канале, можно увидеть выход, в недоработанной такого нет:
Теперь насчет направляющих. Тщательно взвесив все за и против, решил остановиться на своем варианте и пилить ее сложно-пространственно
Для начала разметил на ней метчиком линию, по которой она торчит в канале, также по всему периметру (чтоб легко точить и потом запрессовывать) прочертил ее перед и зад.
Смысл был в том, чтобы максимально
снять торчащего металла, и в то же время оставить по
максимуму по площади канал изнутри (масло) и не трогать
вообще ее нагруженную сторону (разобъет), и при этом все
максимально аэродинамично сгладить.
Впускные
получились по оконцовке такими:
Как видно, на пятке (та сторона, на которую давит при работе клапан) я практически не трогал металл, поэтому вряд-ли деформируется.
С выпускными немного тяжелее — там и отвод тепла и нагруженность сильнее, и направление потока больше. Поэтому смысл такой-же, но объем работ значительно меньше:
Вот так торчит стандартная (тока покоцанная немного) в обработанном впускном канале:
вот так — обработанная (правда не до конца выведена, это бушная, я ее точил на пробу)
Доработал клапана…
Тяжеловато
было, резец очень плохо берет, даже победитовый… Новый
выпускной клапан практически вообще не берется, мне
советовали на доработку брать только б/у, они лучше
точатся — материал мягче.
Зато потом зажал в дрель и
доводил форму шкуркой — берется на ура! Медленно зато
уверенно снимается металл.
Вот что получилось в
итоге:
Снимался металл вот так:
(обработанная фотка стокового впускного клапана, красным — снятый металл)
Запрессовал направляющие изготовленной оправкой (стальной прут, внутри отв. 11.0мм) Голова в духовке до 100 град, направляющие в морозилку. Забивать надо аккуратно, но очень быстро. Не забыть снять шпильки распреда, они будут мешаться (без снятия крайних вообще не запрессовать). Сначала лезет легко потом нагреваются, но все равно лезут нормально. Выбивались, чесслово, с гораздо большим усилием. Главное, шустрее орудовать.
Фото впуска с клапаном:
Выпуск с клапаном
ГТЖ вместо 135/125 ввинтил 140/140. Немного покатался для небольшой приработки, померился.
Как и следовало ожидать, ровный рост КМ
по всей кривой, увеличение оборотов ММ, увеличение КП.
Прибавка получилась 14 лошадей (ну или 12, если
учесть, что в молодости мотор имел 75), на что
предварительно и рассчитывалось.
Ну, думаю, окончательной тарировкой карба еще одну-другую лошадку сниму (поскольку вроде и так едет нормально, без провалов)
Если все мои изыскания сжать в единый временной промежуток и выбросить эстетику (вроде надраивания до блеска головы), то в 5 рабочих дней уложиться можно легко. 1 день — снятие-установка-настройка, 3 дня пиления и 1 день на расслабоне посвятить можно клапанам.
Источник: www.vaz.ee
Автор: Андреем Кушпелем (Oxygen)
|
|
|
Читайте также:
Доработка ГБЦ (ВАЗ)
Переделка 8 клапанной ГБЦ карбюратор в 16 клапанный инжектор
16 клапанная головка цилиндров: установка распредвалов с большим подъемом
16 клапанная головка цилиндров: доработка каналов
ГБЦ 8v: 39×34 + каналы
the-racer-edge.narod.ru
Доработка ГБЦ ВАЗ 2101, 2103, 2105, 2106, 2107
Конструкция и подготовка головки блока цилиндровГоловка блока цилиндров двигателя вместе с цилиндром образует надпоршневую полость, в которой осуществляются все тепловые процессы рабочего цикла. Сложность конструкции головки цилиндров обусловлена множеством функций, которые она выполняет, а также рядом требований, предъявляемых к ней:
- обеспечение формы камеры сгорания, способствующей улучшению процесса сгорания для достижения максимальных значений среднего эффективного давления;
- достаточная жесткость и прочность;
- возможность размещения распределительного вала;
- плавность переходов и равномерность толщин стенок для увеличения надежности при действии механических и тепловых нагрузок;
- обеспечение минимального сопротивления во впускном и выпускном трактах;
- обеспечение равномерной циркуляции охлаждающей жидкости при более интенсивном охлаждении наиболее горячих стенок вокруг выпускного канала;
- возможность размещения впускного и выпускного патрубков и другого вспомогательного оборудования.
Головка цилиндров двигателя М-412 выполнена из алюминиевого сплава АЛ-4 с твердостью не менее НВ 75. Хорошая теплопроводность алюминиевого сплава предопределяет возможность форсировки двигателя, связанной с повышением тепловой напряженности головки цилиндров и оборудования, размещенного на ней.
Спортсменам, выполнившим спортивный разряд и дошедшим до финиша нескольких соревнований за счет надежности стандартного двигателя, пора задуматься о повышении динамики автомобиля и повышении его максимальной скорости.
Первое мероприятие в этом направлении всем хорошо известно — это повышение степени сжатия путем фрезерования плоскости разъема головки цилиндров за счет уменьшения объема камеры сгорания.В табл. 28 приведены расчетные значения степени сжатия двигателя М-412 для различной глубины фрезерования головки цилиндров. (Степень сжатия стандартного двигателя М-412=8,8) .
Таблица 28
Зависимость степени сжатия двигателя М-412 от глубины фрезерования головки блока
Глубина фрезерования,мм | 0,5 | 0,8 | 1,0 | 1,2 | 1,4 | 1,6 | 1,8 | 2,0 |
Степень сжатия | 9,25 | 9,64 | 9,83 | 10,09 | 10,48 | 10,81 | 11,62 | 12,85 |
Таблица 29
Зависимость степени сжатия двигателя ВАЗ-21011 от глубины фрезерования головки блока
Глубина фрезерования,мм | 0,2 | 0,5 | 0,8 | 1,0 | 1,2 | 1,5 | 1,8 | 2,0 | 2,5 | 2,9 |
Степень сжатия | 9,0 | 9,2 | 9,4 | 9,5 | 9,8 | 9,9 | 10,2 | 10,4 | 11,0 | 11,5 |
Завод ВАЗ выпустил головки блока с тремя маркировками, отлитыми с левой стороны над плоскостью разъема. Головки с маркировкой 2101-1003015 и 21011-1003015-10 (унифицированная головка, устанавливаемая в настоящее время на двигатели всех моделей) имеют одинаковый объем камеры сгорания- 32 см3. Головка блока с маркировкой 21011-1003015 устанавливалась до середины 1976 г. только на двигатели ВАЗ-21011. Это следует учитывать при комплектации деталей для сборки двигателя.
У двигателя ВАЗ-2106 поршень не доходит до верхней плоскости блока 1,9 мм (у ВАЗ 21011-0,1 мм), поэтому в табл. 30 приведены значения степени сжатия в зависимости от глубины фрезерования не только головки блока, но и самого блока или головки и блока вместе. Фрезерование головки блока более чем на 3 мм опасно с точки зрения вскрытия водяных каналов.
Обе таблицы составлены с учетом заводской комплектации в настоящее
время, т. е. имеется в виду установка унифицированной головки на все
двигатели. Поршни в двигателях ВАЗ-21011 имеют плоское днище, а поршни
ВАЗ-2106-с проточкой на днище (объем этой проточки 1,7 см3).
Лучше
всего фрезеровать полностью разобранную головку цилиндров, т. е. без
всасывающего и выхлопного патрубков, бензонасоса, распределительного
вала и всей системы газораспределения, но с закрепленной крышкой
шестерни привода распределительного вала (М-412).
Фрезеровать желательно на вертикально-фрезерном станке фрезой, которая всю плоскость головки по ширине может пройти за один проход. Впрочем, годится любая другая технология фрезерования при условии, что чистота обработки плоскости головки будет не хуже производимой заводом-изготовителем. Как правило, опытный фрезеровщик проходит плоскость головки 2 или 3 раза независимо от выбранной глубины фрезерования. Делается это во избежание ошибок, которые потом трудно исправить. После закрепления головки на станке проверяется правильность ее установки по уровню. Первый проход- проверочный — осуществляется на меньшую глубину, чем предполагаемая для выбранной степени сжатия. Если после первого прохода высота головки цилиндров по всему периметру одинакова (исходный размер стандартной головки-108,5 мм), то можно уверенно производить окончательную обработку.
После фрезерования снимаются заусенцы и головка тщательно очищается от стружки. Желающим произвести подготовку головки блока цилиндров по программе максимум, однако, рано думать о сборке головки и постановке ее на двигатель. Надо на расточном станке произвести тонкую и сложную работу по расточке седел для клапанов увеличенного диаметра (рис. 33, 34, 35).
Улучшение условий наполнения цилиндров горючей смесью и очистки их от продуктов сгорания, осуществляемое за счет постановки увеличенных клапанов (рис. 36), дает прибавку в мощности на 5 л. с., как было специально замерено на испытательном стенде Центрального института топливной аппаратуры на стандартном двигателе М-412.
Алюминиевые головки цилиндров всех автомобильных двигателей
изготавливаются со вставными седлами под клапаны из высокопрочного
жаростойкого чугуна, имеющего высокий коэффициент расширения. Чтобы
плотно и надежно посадить вставные седла в головку, ее нагревают
примерно до 170-220° С, а седла охлаждают до температуры сухого льда
-80° С.
На двигателях ГАЗ после такой сборки седла еще обвальцовывают
путем уплотнения вокруг них материала головки. Это необходимо делать,
потому что наиболее горячим местом головки является перемычка между
гнездами седел клапанов, нагревающаяся до температуры выше +200° С. Так
как механическая прочность алюминиевых сплавов при нагреве снижается, то
плохая посадка вставного седла может привести не только к потере
герметичности, но и к выходу из строя всей головки.
Проточить седла клапанов под нужный размер проще, если они отделены от головки цилиндров. Но как после этого снова надежно запрессовать седла в головку, если уже нарушены посадочные места при выпрессовке? Поэтому и рекомендуется расточка седел непосредственно в головке блока, хотя для этого потребуются специальные победитовые резцы и приспособления, позволяющие растачивать седло соосно направляющей втулке клапанов. Одновременно фаска седла всасывающего клапана делается под углом 30° вместо 45°.
Для тех же целей, т. е. для улучшения наполнения цилиндров и создания минимального сопротивления выхлопным газам, производится обработка всасывающего и выхлопного каналов головки цилиндров, а также соответствующих патрубков. Самого материала головки при этом снимать много не приходится, так как каналы кроме приливов для запрессовки направляющих втулок клапанов имеют достаточное проходное сечение. Практика показала, что укороченные направляющие втулки вполне работоспособны (не наблюдалось повышенного износа по внутреннему диаметру, как предполагалось ранее), а каналы головки цилиндров приобретают хорошую геометрическую форму.
Выступающие в каналы части направляющих втулок срезаются на
сверлильном станке сверлом диаметром 22-25 мм на малых оборотах со
стороны седла клапана. Доводка чистоты клапанов головки делается набором
шарошек, а затем наждачной лентой, закрепленной в патрон электродрели.
Аналогично производятся работы с всасывающим и выхлопным патрубками.
Следует
особо отметить, что значительные потери в мощностных показателях
двигателя появляются при неточной стыковке каналов головки с
соответствующими патрубками. При обработке каналов головки на это сразу
надо обратить внимание, подогнать по месту все прокладки и ликвидировать
уступы за счет подгонки патрубков, не трогая подготовленные каналы
головки.
До сих пор речь шла о комплексе работ по подготовке головки цилиндров для стандартного двигателя. Все эти работы остаются необходимыми и при подготовке головки цилиндров для двигателя с увеличенным рабочим объемом, но появляется необходимость дополнительных обработок и меняется их порядок.
После установки гильз цилиндров и поршней диаметром 92 мм
стандартная головка М-412 может быть использована лишь с частично
заваренными водяными каналами вокруг камеры сгорания во избежание
нарушения герметичности и прорывов газов в систему охлаждения.
Уменьшение
сечения каналов охлаждающей системы в этом случае не имеет значения,
так как интенсивность циркуляции охлаждающей жидкости по-прежнему будет
лимитироваться проходным сечением отверстий прокладки головки цилиндров.
Конструктивно вновь наваренный материал головки оказывается напротив
торцов гильз цилиндров и является поэтому опорной поверхностью при
зажатии головки цилиндров на блоке. Это обстоятельство обусловливает
значительные напряжения в сварочном шве и предъявляет особые требования к
качеству дополнительной наварки в местах соединения с основным
материалом головки.
Горький опыт испорченных головок цилиндров и
выхода из строя двигателей в ряде случаев из-за откалывания наваренного
алюминия помог отработать следующую технологию.
Сначала фрезеруется
плоскость головки на 2-2,5мм, затем провариваются водяные каналы, а
после этого проводится уже окончательное фрезерование до глубины 3-5 мм в
зависимости, от выбранной степени сжатия.
В связи с использованием поршней с плоским днищем зависимость степени сжатия от глубины фрезерования для двигателя с рабочим объемом 1870 см3 меняется по сравнению со стандартным двигателем следующим образом (табл.31):
Таблица 31
Глубина фрезерования, мм | 2,0 | 2,5 | 3,0 | 3,5 | 4,0 | 4,5 | 5,0 | 5,5 |
Степень сжатия | 8,81 | 9,18 | 9,38 | 9,66 | 10,1 | 10,6 | 10,8 | 11,5 |
Для обеспечения свободного прохождения поршнем ВМТ в каждой из четырех камер сгорания головки делается коническая выточка с наружным диаметром 92 мм (см. рис. 33). Сделать эту выточку полностью на фрезерном или расточном станке нельзя, так как на ее пути лежит седло всасывающего клапана. Поэтому на станке выбирается металл до тех пор, пока фреза или резец не приблизится к седлу. Остальную работу приходится делать вручную шарошкой. Когда работа подходит к концу, головку надо примерить на собранный блок цилиндров. При этом головка блока, конечно, без всякого оборудования ставится без прокладки и в середине слегка поджимается двумя гайками.
Задача первой примерки — добиться свободного вращения коленчатого вала без следов столкновения поршней с головкой в местах конусной проточки. Чтобы следы столкновения, если они будут, стали более заметны, края днища поршня можно смазать тонким слоем нигрола или гипоидной смазки. При этой же примерке проверяется правильность расположения и глубины выборки на днище поршня. Если она произведена неправильно, на выборке в поршне остается след столкновения с седлом всасывающего клапана. Тогда выборку надо углубить или сместить в сторону.
Как правило, ликвидация всех мест столкновений поршня с головкой сводится к выборке металла в районе седла всасывающего клапана и некоторого углубления за этим седлом. Дело это трудоемкое, требует терпения и аккуратности. Обычно такая подгонка заканчивается после примерки головки цилиндров 10-12 раз. Следующая примерка делается по такой же методике, но в головку предварительно ставят уже всасывающие и выхлопные клапаны. Задача такой примерки (опять без прокладки головки) — проверить, не упирается ли поршень своей выборкой во всасывающий клапан в закрытом состоянии. Если упирается, требуется доработка выборки в поршне; если нет — можно браться за окончательную работу над поверхностью и объемом камеры сгорания.
Считаем само собой разумеющимся, что до Постановки клапанов в
головку они помечены по номерам цилиндров, добросовестно притерты пастой
и проверены обычными методами на герметичность.
Головку цилиндров с собранными клапанами проверяют на величину
объема камеры сгорания, точнее, на величину объема сегментной полости,
часть которой является камерой сгорания (свеча ввернута). Для точного
замера объема используется пластинка размером 25 Х 25 см, толщиной 3-4
мм из оргстекла. В пластинке делаются два отверстия диаметром 4 мм. Одно
для заливки воды, другое для выхода воздуха. Пластинка смазывается
тонким слоем солидола и плотно прижимается к плоскости головки. Такой
замер объема исключает ошибки из-за случайного перелива воды.
В связи
с доработкой конусной выточки вручную неизбежно появится разница в
объемах камеры сгорания (будем пока так называть для простоты изложения
объем сегментной полости), иногда до 3-5 см3.
Подгонка камеры сгорания по объему производится за счет выборки в местах технологических выступов материала головки — между седлами клапанов и вблизи отверстия под свечу. Эту работу можно считать оконченной лишь в том случае, если разница в объемах не превышает 0,5-1 см3. Теперь можно слегка «пошкурить» поверхность камеры сгорания для ликвидации оставшихся рисок — потенциальных центров детонационного горения смеси и мест отложения нагара. Перед окончательной сборкой двигателя можно рекомендовать полировку поверхности камеры сгорания и днища поршня.
Головка промывается бензином, затем водой из шланга под напором и продувается сжатым воздухом. Чтобы не появилась ржавчина на стержнях, тарелках и седлах клапанов, эти места поливаются моторным маслом из тонкой масленки. Дальнейшая сборка головки сводится к установке в нее рокерных валиков с коромыслами, распределительного вала, наконечников клапанов и регулировке (предварительной) зазоров между клапаном и наконечником в пределах 0,2-0,25 мм.
Третья, окончательная примерка производится после подготовки шестерни привода распределительного вала со сдвинутым по фазе отверстием под штифт. После фрезерования головки цилиндров ось вращения кулачкового вала располагается на величину фрезеровки ближе к оси коленчатого вала. Из-за изменения межосевого расстояния между валами обе ветви цепи привода распределительного вала ослабнут, если предположить, что метка шкива коленчатого вала и метка распределительного вала находятся в положении, соответствующем ВМТ первого поршня. Представим себе, что из этого статического положения начинает работать двигатель, т. е. начинает вращаться коленчатый вал. Слабина ведомой ветви цепи компенсируется дополнительной натяжкой промежуточной шестерни, а за счет слабины ведущей ветви распределительный вал начнет отставать на некоторый угол от своего нормального положения (когда метка стоит напротив прилива в головке). Чем больше глубина фрезерования головки, тем на больший угол распределительный вал будет отставать (табл. 32).
Таблица 32
Глубина фрезерования, мм | 0,5 | 0,8 | 1,0 | 1,2 | 1,4 | 1,6 | 2,0 | 3,0 | 4,0 | 5,0 |
Угол отставания распределительного вала | 0,53 | 0,83 | 1,1 | 1,3 | 1,6 | 1,7 | 2,1 | 3,2 | 4,3 | 5,4 |
Компенсировать угол отставания можно поворотом шестерни относительно переднего фланца распределительного вала на тот же угол против часовой стрелки. Но как закрепить теперь шестерню, если не совпадают на этот угол отверстия под крепежные болты и под штифт? Смещение ближайшего отверстия под крепежный болт (в направлении по часовой стрелке) от штифтового отверстия составляет 45°. Рассверливаем его до диаметра 8 мм. под штифт. На фланце распределительного вала все остается на своих местах. Переставляя шестерню на распределительном валу так, чтобы штифт попал в новое отверстие, получаем смещение на 45°, а фактически, передвигая цепь на 4 зуба (по 10°), получаем смещение на 5°. Этого достаточно, так как фрезерование для двигателя М-412 производится обычно на глубину 3,5-5 мм, и при смещении шестерни на 5° метка распределительного вала не выходит за пределы прилива на головке.
Следствием нового способа при постановке шестерни на вал является совпадение лишь одного из четырех крепежных отверстий (бывшее штифтовое). Остальные три сверлятся нужным диаметром. Таким образом, одна такая шестерня «обслуживает» все головки и все распределительные валы. Новое штифтовое отверстие на шестерне лучше сразу пометить каким-либо способом, например, выбить рядом цифру 5 (смещение на 5°), чтобы в дальнейшем при сборке двигателя не создавать себе лишних «поисковых» проблем. Теперь имеется все необходимое для третьей, окончательной: примерки собранной головки цилиндров на блоке. Задача этой примерки, так же как и предыдущей, проверить, не происходит ли «встреча» всасывающего клапана и поршня, но уже в динамике с присоединенной шестерней распределительного вала и цепью.
Если двигатель проворачивается свободно без прокладки головки, то можно гарантировать безаварийную работу его после постановки прокладки. Прокладку головки блока для двигателя увеличенного литража изготавливают, используя прокладку серийного двигателя, так как опыт использования медных прокладок различной толщины (от 0,2 до 2 мм), а также составных прокладок положительных результатов не дал. В стандартной прокладке, на специальном приспособлении вырубаются отверстия диаметром 94 мм. Для металлических колец лучше брать листовую нержавеющую сталь толщиной 0,35-0,4 мм, предварительно отожженную в вакуумной среде. Окантовка отверстий прокладки головки производится на вальцовочном станке. Для двигателей ВАЗ, особенно форсированных до степени сжатия 11,0-11,5, хорошо зарекомендовала себя комбинированная прокладка головки блока, состоящая из колец отожженной красной меди, которые уплотняют камеру сгорания, и стандартной прокладки для уплотнения соединений по системе охлаждения и смазки (рис. 37).
tun-lada.blogspot.com
Ремонт головки блока цилиндров на автомобилях ВАЗ (классика)
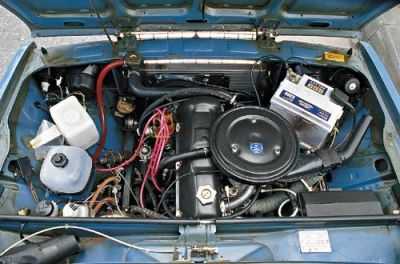
Опытные владельцы классических моделей ВАЗ знают, что безотказно функционирующая головка блока цилиндров является залогом устойчивой и долговечной работы мотора транспортного средства. Кроме того, техническая исправность данного агрегата положительно влияет на расход топлива и динамику движения, что позволяет повысить маневренность и управляемость машины.
Неопытным водителям следует помнить, что ремонт ГБЦ должен производиться только подготовленными профессионалами, в противном случае неправильно отрегулированный узел неизбежно приведет к порче всех деталей двигателя. Капитальное восстановление мотора обойдется в кругленькую сумму, после чего на вопрос, сколько он прослужит, не рискнет ответить даже опытный специалист. Тем не менее, для знающих владельцев классических моделей ВАЗ, которые имеют определенные навыки, выполнить все соответствующие мероприятия по замене головки блока цилиндров можно и своими руками.
Снятие ГБЦ ВАЗ: этапы и инструкции
Безусловно, любой серьезный ремонт детали автомобиля начинается с ее снятия. Перед разборкой не забудьте слить с мотора охлаждающую жидкость, после чего необходимо демонтировать карбюратор и воздушный фильтр, предварительно отсоединив от него все шланги и патрубки.
Следующим мероприятием станет снятие крышки ГБЦ и совмещение меток на шкиве коленвала с риской на приводе распределительного вала, а также метки на шкиве распредвала с риской на его корпусе.
Далее ослабляем натяжитель цепи путем отсоединения стопорной шайбы распределительного вала. Рывком срываем болт и аккуратно демонтируем звездочку в агрегате, привязывая ее к цепи или другими элементам двигателя. Последовательно отворачиваем крепления и снимаем распредвал вместе с корпусом.
Очень важным этапом станет снятие рокеров, которые предварительно нужно пометить маркером, что гарантирует при сборке правильное положение данных деталей. Сами изделия легко вытаскиваются пружин и снимаются с регулировочных болтов. Теперь можно отсоединить провода, ведущие к свечам зажигания и датчикам температуры охлаждающей жидкости. Демонтируем трубу к выпускному коллектору и отворачиваем болты, с помощью которых головка крепится к блоку. Вынимаем ГБЦ и аккуратно очищаем ее от нагара или прочих загрязнений.
Поиск дефектов ГБЦ
Непосредственно сам ремонт головки блока цилиндров на автомобилях ВАЗ начинается с рассухаривания клапанов, для чего используются приспособления, которые изображены на рисунке ниже. В процессе разбора клапаны необходимо пометить и разложить по своим местам, что позволит при условии небольшого износа поставить их обратно.
При внимательном рассмотрении ГБЦ не подлежащей восстановлению на ней должны быть заметны сколы, трещины, признаки коррозии. Оценить следует также и износ направляющих и седел, ремонт которых проводят каждые 200 тыс. километров пробега. Если никаких видимых дефектов на ГБЦ не обнаружилось, то можно продолжать ее дальнейший ремонт.
Замена направляющих втулок
В случае выработки ресурса направляющих втулок их необходимо обязательно заменить. Извлекают такие детали при помощи специального инструмента, однако в гаражных условиях подойдут и плоскогубцы и зажим. При демонтаже втулок сразу же замеряем их наружный диаметр, после чего ищем в специализированных магазина аналоги с размерами на 0,05-0,07 мм больше родных.
Обратная запрессовка направляющих происходит с использованием оправки, электрической плитки, молотка и машинного масла. Головка блока ставится на подставку по краям, после чего электроприбор ставится под место работы и нагревает металл до 100 °С (при такой температуре он начинает расширяться). Смазываем втулку маслом, снимаем с держателей и вбиваем туда новые направляющие. После замены всех восьми составных элементов ГБЦ подлежит охлаждению, а внутренний диаметр разворачивают таким образом, чтобы клапаны не болтались и ходили свободно, без заклиниваний или заеданий.
Зенкование седла головки
Самым мучительным и важным мероприятием при ремонте ГБЦ является замена седла головки, от качественного выполнения которого и зависит степень прилегания клапана к седлу, а также дальнейшая работа мотора. Как правило, снимают слой металла по кругу, затем под углом 120° срезают ГБЦ до момента появления четкой круглой кромки. На финальном этапе выходной шарошкой делают рабочую фаску с толщиной 1,5-2 мм для плотной притирки клапана.
Проверка герметичности ГБЦ
Для того чтобы клапана как можно плотнее прилегали к своим седлам, нужно воспользоваться следующим методом. В любом специализированном магазине приобретаете специальную притирочную пасту, смазываете клапан и вставляете его в головку. При этом известно два способа его вращения:
- при помощи куска шланга, который плотно надевается на деталь;
- при помощи специального ремонтного приспособления, напоминающего штопор.
Главным визуальным показателем притирки клапана станет матовая поверхность седла в месте контакта с проточенной деталью. Герметичность ГБЦ проверяется с помощью заливки во впускной и выпускной коллекторы керосина или бензина. В случае правильно выполненного ремонта течи из-под клапанов не будет первые 5-7 минут работу двигателя.
Напоследок напомним, что все детали мотора ВАЗ при разборке должны промываться особым раствором, что гарантирует долгую и надежную службу силового агрегата на протяжении не одной сотни тысяч километров.
autoremka.ru